Stainless steel stirred tank reactor are the workhorses of the chemical industry, playing a crucial role in the production of a wide range of products, from pharmaceuticals to petrochemicals. These reactors are designed to handle a variety of chemical processes, making them indispensable in modern manufacturing. In this comprehensive guide, we will delve into the inner workings of stainless steel stirred tank reactors, exploring their applications, design considerations, and maintenance best practices.
Stainless steel stirred tank reactors find extensive use in the production of pharmaceuticals, specialty chemicals, polymers, and petrochemicals. Their versatility allows for a wide range of chemical processes, including mixing, blending, dissolution, and crystallization. These reactors are particularly valuable in the pharmaceutical industry, where they are used for synthesis, purification, and isolation of active pharmaceutical ingredients (APIs). Additionally, in the petrochemical sector, stainless steel stirred tank reactors play a critical role in processes such as polymerization and hydrogenation.
The design of a stainless steel stirred tank reactor is a complex task that involves considerations such as material selection, agitation mechanisms, heat transfer, and pressure handling. Stainless steel is the material of choice due to its corrosion resistance, durability, and ease of cleaning. The agitation system, typically consisting of impellers and baffles, plays a crucial role in promoting mixing and heat transfer within the reactor. Furthermore, efficient heat transfer is facilitated through the use of jacketed or coil-wrapped reactors, allowing for precise temperature control during chemical processes.
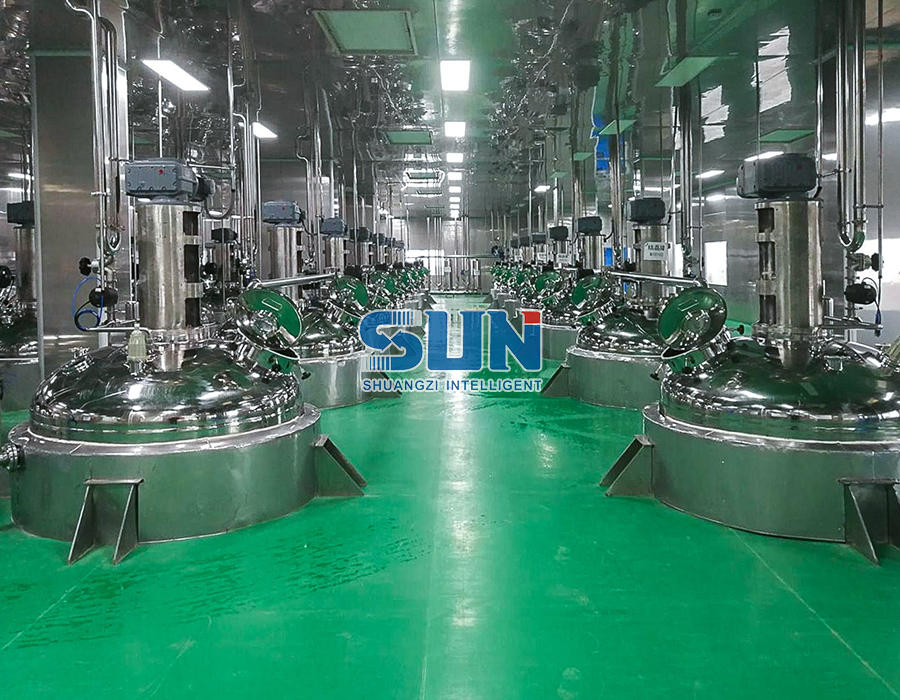
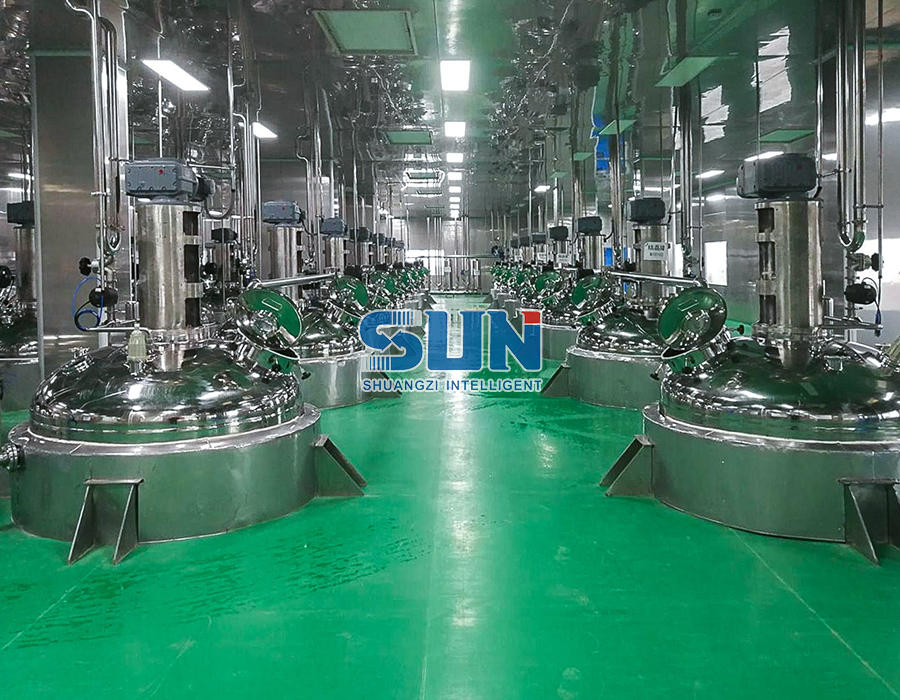
Proper maintenance is essential to ensure the longevity and optimal performance of stainless steel stirred tank reactors. Regular inspection of internal components, such as agitators and baffles, helps identify wear and tear that may affect mixing efficiency. Additionally, thorough cleaning and passivation of the stainless steel surfaces prevent corrosion and maintain the hygienic standards required for pharmaceutical and food processing applications. It is also crucial to monitor and maintain the integrity of the reactor’s seals and gaskets to prevent leaks and ensure process safety.
Stainless steel stirred tank reactors are indispensable tools in the chemical industry, serving a wide array of applications with their robust design and versatile capabilities. Understanding the applications, design considerations, and maintenance best practices for these reactors is essential for maximizing their efficiency and ensuring product quality and safety. By adhering to best practices and leveraging the capabilities of stainless steel stirred tank reactors, manufacturers can achieve optimal process performance and meet the stringent demands of modern chemical production.